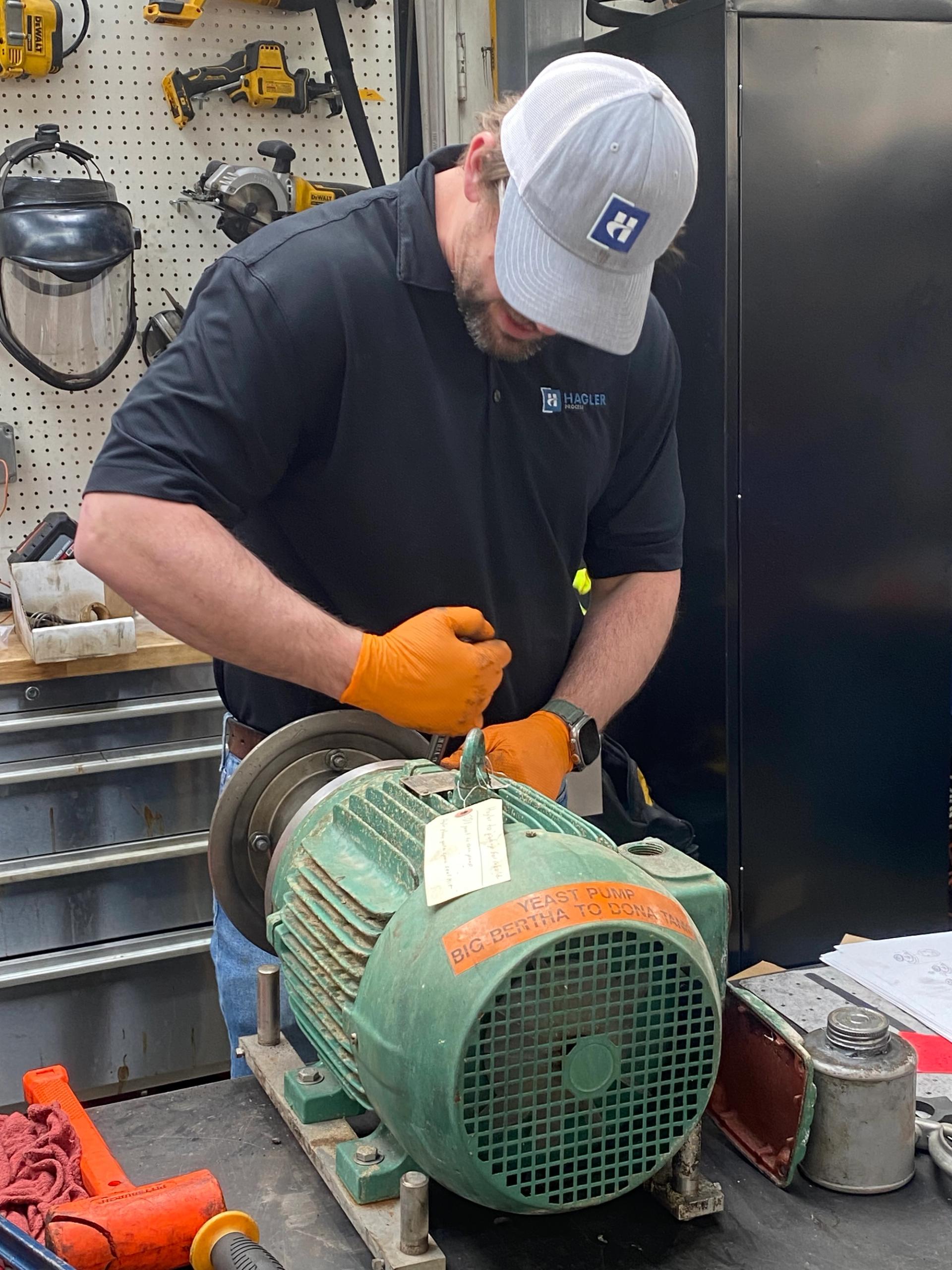
Custom Pumping Systems for a Detergent Plant in the Health & Beauty/Chemical Process Industry
A customer in the health and beauty industry contracted Fischer Process Industries to develop a Custom Pumping Systems for a chemical process in their detergent plant. The customer was currently using our smaller version of the pump, and wanted to increase their capacity and add mixing centers. We performed an analysis of their process dynamics, and developed the specifications outlining the pumps, motors, and gearboxes necessary to increase their process of multiple product detergents. Our engineers also designed custom base plates for fabrication.
Product Name:
Waukesha Pumps
Product Description:
Positive Displacement ECP Lobe Style Pumps
Custom Pumping Systems Capabilities Applied/
Primary: Engineering
- Analyzed the process dynamics, developed pumps, motor, gearbox specification and designed custom base plates for fabrication
Material Worked With:
Multiple Product Detergents
In Process Testing/
Functionality Testing
Documentation Supplied:
Approval on 3D Dimensional Drawings, Engineering and Operations Manuals
Industry for Use:
Health and Beauty/Chemical Process
Volume:
Five (5) large 6" Positive Displacement ECP Lobe Style Pumps
Delivery Location:
Bowling Green, Kentucky